自動車用バスバーは、EV(電気自動車)やHEV(ハイブリッド車)などの電動化が進む中で、その重要性がますます高まっています。大容量の電流を安定的に供給するバスバーは、車両の効率的なエネルギーマネジメントを支える中核部品のひとつで、今後、電動化の加速に伴い、その需要はさらに拡大することが予測されます。
本記事では、自動車用バスバーの「基礎知識」から「最新技術動向」までをわかりやすく解説します。設計・選定時に重要な「素材の選定」「加工技術」「防水性」「リサイクル対応」などのポイントを、車両のパフォーマンスや信頼性に与える影響とともに、具体的に掘り下げていきます。
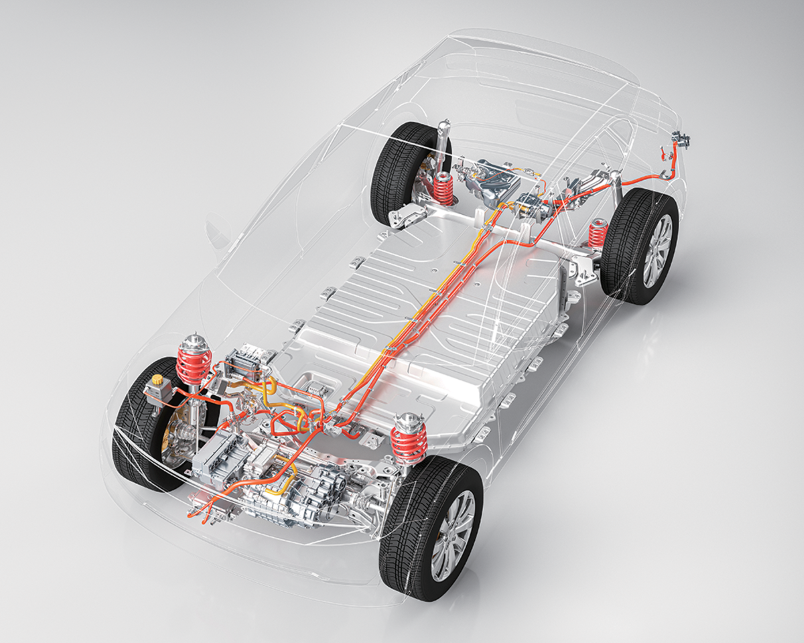
1.バスバーとは? 自動車における役割・メリットと重要性
主に銅やアルミニウムなど、高い導電性を持つ金属を使用し、大電流を安全かつ効率的に伝送する「金属製の配線部材」がバスバー(ブスバー)です。
近年、バッテリー(電池)やインバータ、モーターなど、高電圧を扱う部位が車両内に増加し、電装系統はますます複雑化しています。その結果、従来のケーブル配線では対応しきれない場面が多くなってきました。限られたスペースでも配線をすっきり整理でき、放熱性にも優れるバスバーは欠かせない存在となっています。
バスバーの概要と必要性
自動車におけるバスバーは、ケーブル配線に比べて、よりコンパクトかつ効率的に配電・大電流を取り扱える配線方式として注目を集めています。
特にEVやHEVなどの電動車両では、車載制御盤や電力系統全体で電力ロスを抑え、エネルギー効率を高めるうえで、バスバーが重要な役割を担っているのです。さらに、構造がシンプルで、保守や点検がしやすいため、長期的なメンテナンスコストの削減にもつながると期待されています。
2.自動車用バスバーの主要素材と表面処理
銅・アルミ・複合材のそれぞれの特性比較
銅は導電率・熱伝導性ともに優れており、特にタフピッチ銅(TPC)や無酸素銅(OFC)は電気的性能から自動車用バスバーで広く使用されています。
一方、アルミニウムは比重が銅の約1/3と軽く、車両の軽量化が求められるEVやHEVでの採用が進んでいます。導電率は銅より劣るものの、コストの低さや軽さによる航続距離の延長といった点で大きなメリットがあります。
さらに、銅とアルミの複合材(クラッド材など)は、それぞれの長所を融合することで、高耐久かつ軽量という相反するニーズを両立できます。用途や性能要件に応じて柔軟に対応できる次世代素材として、今後ますます注目されるでしょう。
バスバー表面処理の種類
バスバーの表面処理には、使用環境や求められる性能に応じて適切な方法が選ばれます。代表的な表面処理方法には、すず(錫)めっき、ニッケルめっき、絶縁塗装(コーティング)があり、それぞれに特徴があります。
すずめっき:接触抵抗を低減することで、接触部での熱の発生や腐食の抑制を実現します。特に、低電流時や高頻度で接続が外れる場面で効果を発揮します。
ニッケルめっき:優れた耐食性を持ち、湿気や化学物質にさらされる過酷な環境下でも安定した性能を提供します。また、高温にも強いため、車両内の熱環境が厳しい場所にも適しています。
絶縁塗装(コーティング):配線同士のショートや漏電を防ぐために重要です。安全性を確保するため、特に高電圧を取り扱う車両においては、不可欠です。
さらに、超音波金属接合機を使用すれば、表面処理されたバスバーでも接合可能です。すずめっきやニッケルめっきが施された状態でも、接合部のめっき層(酸化被膜や吸着ガスなどの表面層)を機械的に破壊除去しながら接合できます。同時に、発生する摩擦熱により組成流動が促進され、接合界面の原子同士が結合するため、導電性に優れた接合を実現できます。複雑な前処理を必要とせず、高品質な電気接続を可能にする、注目の工法です。
「超音波金属接合機」を詳しく見る
3.バスバーの製造工程と加工技術
バスバーの製造工程や加工技術の選定は、品質の確保はもちろん、生産効率やコスト競争力に直結します。特に自動車用バスバーでは、車両の構造やレイアウトに応じて多様な形状や仕様が求められるため、切削・プレス・曲げ加工などの複数の加工技術が組み合わされます。
プレス加工・ベンダー技術のポイント
従来、大型のプレス機を使用した量産が主流でしたが、最近では小型で柔軟な設備を導入する企業も増え、多品種少量生産への対応が進んでいます。これにより、複雑な形状のバスバーの製造も可能となり、設計の自由度が増しています。
特に曲げ加工では、角度や曲げ半径の正確さが求められます。これを達成するためには、熟練の技術者の経験と、精密な制御が可能な最新の自動化システムの両方が欠かせません。こうした技術により、安定した製品品質が保証されるのです。
マルチフォーミング加工による材料歩留まり向上とコスト削減
マルチフォーミング加工とは、切断・打ち抜き・曲げなど複数の工程を一貫して自動的に行う高度な加工技術です。この連続加工により、材料ロス(歩留まり)の低減や生産効率の向上が可能となり、製造現場におけるコスト削減に貢献します。また自動化との親和性が高く、省人化と品質安定を同時に実現できます。
4.バスバーの活用事例と防水・絶縁対策の重要性
車載環境にさらされるバスバーには、高い防水性や絶縁性が求められます。これは、バスバーが車両の電気システムおよび電気系統の中核を担っており、安全性や信頼性に直結するからです。
自動車は極端な温度変化や高湿度、振動や塵埃など過酷な環境下で使用されるため、厳格な品質管理が欠かせません。車両内部といえども完全密閉とは限らず、水滴や塵が入り込む可能性があります。こうしたリスクに対応するため、防水コーティングや絶縁塗装に加え、シール材の活用や多層構造の設計など、複数の技術が組み合わされています。
インサート成形接合による防水性と絶縁性の強化
インサート成形接合は、金属製バスバーと樹脂を一体化させる技術であり、車載配電盤の信頼性向上にも寄与します。成形時にバスバーを樹脂に直接組み込むため、接合部からの水分や湿気の侵入を防ぐことができ、漏電リスクや腐食リスクを低減します。また、樹脂による補強効果で、機械的強度や耐熱性も向上し、激しい振動や温度変化にさらされる自動車の走行環境下でも、長期間にわたって安定した性能を維持します。
5.ケーブル VS バスバー:配線方式の比較
大電流を扱う車載システムでは、ケーブルとバスバーのどちらを採用するか、電力の分配効率や放熱性、スペース効率、メンテナンス性などさまざまな観点から比較する必要があります。
また、取り付けや製造コストにも違いがあるため、どちらを選ぶかは車両の設計方針や生産体制などを考慮したうえでの判断が求められます。
放熱性・スペース効率・コスト面の検討
ケーブルは柔軟性が高く、車体内部の複雑なルートにも適応しやすい一方で、断面積が大きくなると熱がこもりやすいという課題を抱えています。対してバスバーは、複数の回路を効率よくまとめ、省スペース化を実現します。平板状で放熱性に優れ、大電流を効率的に伝送するという特徴があります。ただし、形状変更の柔軟性には制限があり、車両設計の自由度が少し制限されることがあります。
コスト面では、電流容量や放熱性の要件を踏まえた設計が求められます。製造や取り付けにかかるコストにも配慮が必要でしょう。例えば、超音波金属接合機を用いたバスバー接合では、主なランニングコストが電気料金のみで済み、消費エネルギーも少ないため、電気抵抗溶接と比較しておよそ1/5~1/20程度のコストに抑えられるケースもあります。こういった要素のバランスを考慮し、コストも含めて最適な配線方法を総合的に判断することが重要です。
環境負荷もコストも削減!超音波金属接合はこちら
6.バスバーの安全性と環境への影響
自動車部品として重要な役割を果たすバスバーは、その故障リスクを低減しながら、同時に環境にやさしい設計が求められてます。
バスバーは大電流を扱うため、損傷やショートが発生した際には深刻なトラブルを招くおそれがあり、遮熱設計や表面処理の最適化、さらに配線レイアウトの工夫が不可欠です。また、自動車開発段階から素材のリサイクルや廃棄後の処理方法を計画することにより、環境負荷を最小限に抑えることができます。例えば超音波金属接合であれば、接合界面にフラックスなどの介在物を用いずに、バスバーとケーブルを接合できるため、金属素材を分別・再資源化しやすく、リサイクル性に優れています。さらに、接合時に有害なガスや異臭が発生しないという点でも、環境にやさしい加工方法として注目されています。
故障リスクとメンテナンス性
バスバーの継ぎ目や端子部は、故障リスクが高い箇所とされており、接触不良や金属疲労によるトラブルが発生する可能性があります。これらの問題を未然に防ぐためには、定期的な点検や熱画像検査(サーモグラフィ)による異常の早期発見が重要です。特に、異常発熱や端子部の変色が見られる場合には、迅速な対応が求められます。
また、メンテナンス性の向上には、製造段階から分解・再装着が容易な設計を取り入れることが有効です。
リサイクル対応とサステナビリティ
銅やアルミは高いリサイクル特性を持つ材質であり、多くのメーカーが資源の再利用を前提とした設計方針を採用しています。使用済みバスバーや自動車部品を再利用することで、一次資源の採掘による環境負荷を抑えながら、製造コストの削減にも寄与します。
近年では、リサイクル効率を高める新技術や、複合材料からの素材回収技術の開発も進んでおり、自動車業界全体のサステナビリティ向上が期待されています。
7.最新技術動向と今後の展望
自動車の電動化ニーズの拡大により、高性能バスバーへの需要は年々高まっており、各メーカーは生産体制の強化を急ピッチで進めています。また、耐久性と軽量化を両立させる次世代素材の研究開発も活発で、エネルギー効率に優れた製品が次々と市場投入されています。今後は、高電圧対応や省スペース化といった要件に応える先進バスバー技術が、車両開発の重要な鍵を握ると見られています。
高電圧化・軽量化に向けた新素材開発
EVやPHEVの高出力化・大電流化が進む中、高電圧環境に対応可能な新素材の開発が急務となっています。近年では、金属合金の改良や樹脂とのハイブリッド構造によって、薄型かつ高剛性の実用化が進んでいます。
また、車両全体の軽量化は、一充電あたりの走行距離を延ばすうえで欠かせない要素です。特に長尺バスバーや大面積の導体部品においては、軽量かつ高耐久な素材の採用が加速しており、走行性能とエネルギー効率の向上に貢献しています。
多様な製造方法の進化
近年、3Dプリンティング(積層造形)やレーザー加工、樹脂との一体成形技術など、革新的な加工技術が台頭しています。これらの次世代製造プロセスにより、複雑な立体形状の一体成型が可能となり、車両設計の自由度が大きく向上しています。
特に熱マネジメントの最適化や部品点数の削減による軽量化・省スペース化が図れる点は、EV・HEVなどの電動車両開発において大きなメリットです。これらの技術革新は、バスバーの形状最適化・高機能化に貢献し、今後の自動車電装部品業界全体の進化を支えるキードライバーとなるでしょう。
なお、弊社ではこうした新素材に対する接合テストにも対応しており、超音波金属接合機を用いた検証が可能です。開発段階における導入可否の判断や、最適な接合条件の確認など、お客様のニーズに応じた評価サポートを行っています。
お客様の素材で実証できます。接合テストお申込みはこちら
8.まとめ
バスバーは、電動車両に欠かせない重要な配線部品です。
本記事で紹介した通り、大電流を効率的に伝送できる構造や、放熱性・スペース効率に優れた特性から、従来のケーブルに代わる存在として、バスバーの利用が拡大しています。
さらに、素材選定の工夫や高度な表面処理、樹脂との一体成形や3Dプリンティングなどの先進加工技術により、軽量化・高耐久化が加速しています。加えて、自動車の使用環境に求められる防水性の向上や、資源循環を意識したリサイクル対応など、サステナビリティの観点からもバスバーの技術革新は今後も重要なテーマとなるでしょう。